CamSoft's
PC-Based CNC Machine Tool Control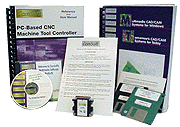
for Windows is a software and/or hardware toolkit that allows you to create and customize
your own controller for any 2 to 8 axis CNC machine tool using a standard personal
computer. Whether it is a retrofit or a brand new machine tool, CamSoft has the answer for
you. All controllers are user configurable and are equipped with CamSoft's Advanced System
3000 Multimedia CAD/CAM for Windows Level 1 software.
Visit our PC Based Machine Tool website at WWW.CNCCONTROLS.COM
We have perhaps the industries fastest and easiest, most full featured CNC controllers offered in todays market. The obvious benefit is a consistency from machine to machine, a standard utilizing one software package for all CNC and General Automation machine types. When you become proficient at CamSoft you will not need to continually address learning curves when you create new applications for different machine types.
Do it your self software/hardware components
-or-
Full service installations and custom solutions.
Priced right, if quality and low cost is what your looking for
-or-
Upgraded packages for people that want the best to handle the most complex applications.
Packages for the OEM, Retrofitter, System Integrator or End user.
-or-
The end user self installation.
Turn key, ready to mount professional CNC enclosures.
-or-
separately sold software and hardware components.
Hardware based motion cards.
-or-
Software based Servo&Stepper drivers.
How does the cost compare?
CamSoft can convert any existing CNC machine at a much more reasonable cost than any
other brand name pre-fabricated control. Prices begin at $2,850 for a 3 axes machine tool. This includes complete hardware and software using your own personal computer. Use our e-quote form to get information fast!
How open is your control?
Servo loop closed in software or hardware
HMI, CNC, Digital I/O, Analog and Logic in one software package
No third party SoftPLC language to run or buy
No Visual Basic or C++ required
Open enough for many first time users to do self installation
Software bundled or unbundled from hardware
API, DLL, ActiveX, Network or RS232
Unlimited real-time data collection
Remote operation and machine monitoring
Self diagnostics tests for motors, analog, encoders and I/O
Automatic servo tuning software
Table of 199 user definable G & M codes
Create and customize G & M codes without using VB or C++
Create and customize hundreds of specialized macro routines
Dozens of logic examples for many types of hardware
Provided Tool changers, Homing routines, Jogging devices, Turrets & Rotary tables
Provided Gear changing, Probes, HandWheels, Canned cycles & Timed events
Provided Blade/Knife functions & Material height sensing
Hundreds of fixture, tool and part offsets
Single operating system environment
No need to run or buy third party kernels or operating systems
Single or Dual CPUs. One for the HMI and one to close servo loop
No proprietary hardware
Use a motion card or use a software driver
Multiple sources for hardware
Industrial or office PCs supported
User Installable and upgradeable
User configurable operator interface
User configured hardware
Supports user independence
Do you offer a turnkey system?
If you want the best the industry has to offer using
a turnkey CNC control installed by a professional, we
offer different ready-to-go, bolt-on professional CNC
controller
enclosures. You also have a choice to install the
same high-quality hardware/software components in our retrofit
kit into your own Windows based personal computer. Visit
our Enclosures page to see the latest products.
How easy is the CNC to install?
A CamSoft machine conversion can be accomplished without the need for you to trace wires to the PLC or write ladder logic. Instead, the computer becomes the PLC and does the logic. We have several ready to go operator screens to choose from and fewer wiring headaches because now you can forget about tracing down the old wires and just run new wires directly from your existing motor drives, encoders, spindle drive, limit and home switches directly to the silk screened and labeled terminal strip we provide you. The software allows you to mix and match physical buttons, knobs, gauges, switches, lights, and displays with virtual ones.
How easy is the CNC to use?
As easy as you would like. The operator screen is fully customizable. We offer several default operator screens for several machine types to get you going. You can make the screen as feature rich or as simplistic as you would like. We offer two programming styles: G code or CAD to motion. You don't have to be a C++ or VB programmer to configure the screen. You simply drag and drop control objects around the operator screen and set their size, caption and functions with fill in the blank or check boxes within Windows to design an operator interface.
Can we use our existing motors and drives?
Yes, it is much easier to use the existing motors and amplifiers. This holds down the cost and labor plus ensures that the motors and amps are sized right for your machine. Our software can control existing motors that are: Brush or brushless, AC or DC, servo, stepper, PWM or hydraulic. The amps, also known as drives, can be either current driven or velocity type. Spindle drives use current mode or invertors. Feed back can be closed loop or open. Closed loop systems use encoders or resolvers. There are a number of companies that make digital I/O cards. Any manufacturer's I/O card that uses a 8255 chip will work. We also have touch screens or we can show you where you can find your own.
How long will this take?
Most companies cannot afford to take months "off" to get a machine on-line and productive. The learning curve with the CamSoft software is approximately 1/5 of the time needed when compared to most CNCs that use PLCs. Installation can be done in 3 days for most common types of knee mills, bed mills, lathes, lasers, water jets, plasmas and punch presses. Ask us to send you our 3 day installation info e-mail or flyer.
Where is the retrofit done?
Another issue is convenience and shipping. If you have a large machine, you don't want to truck it all over creation. You can do the installation yourself, in your own shop, within your own timeframe or have one of our people come to you on an as-needed basis. Do what you can to save time and labor costs and call us to finish the rest.
Will our old G code programs still run?
Yes, you can have the controller run a Fanuc G code program in the morning and then an Allen Bradley in the afternoon. We give you a definable G code and M code table to allow you to configure the new controller to understand your pre-existing programs.
Can we customize the system ourselves?
Yes, you can customize the complete system. This is an open system. The screen can be customized without having to be a VB or C++ programmer. Typical Windows style fill in the blanks and check boxes are used on well organized screens so that even novice Windows users can drag and drop objects into place and set their properties. More advanced users will be able to configure the controller routines to support new processes and new technologies with published, well-documented software application program interfaces (APIs) made available to all customers as well as source code for ActiveX and DLLs.
How fast is the CNC performance?
The hardware is tested and proven with over 200,000 motion cards shipped to date. 62.5 microsecond servo update times per axis result in cutting feedrate velocities of up to 122,000 IPM which is far greater than today's servo motor technology. With our auxiliary digital I/O cards you can detect a change of state at rates in the 10 Khz range. DSP ASIC, digital signal micro-processors with application specific integrated circuits to close the servo loop, use dual 32 bit processors to increase productivity, feedrates, accuracy and cut quality. Multiple events and multiple position motions can happen simultaneously. 3D profiles can be cutting while the tool is changing or a servo motor positions a rotary table. The extra processor on the motion card is not only the best way to close the servo loop with the motors, it is also the fastest method known to date to produce the fastest block-to-block cutting speeds.
Third party support and communications?
The software supports the ability to integrate third-party applications into the machine control. The standard software already includes machine maintenance software, remote diagnostics via a modem, self diagnostics and remote machine tool monitoring via RS232, ActiveX or Network card. This includes automatic collection of manufacturing data in real time without operator intervention such as cycle time, feed rates, and setup time as a standard feature.
Will this help eliminate downtime?
The idea of being able to replace the controller with a spare computer is a good one. There will be a terminal strip that connects the machine wiring to the computer via a 100-pin cable. To swap out the old computer with a new computer, unplug the cable from the computer. This will not disturb the wiring to the machine. Next, you will have a single backup file called a CBK file. This file will fit onto a floppy disk and is small enough to be e-mailed. The customer can restore the screens and logic to a new computer within 10 seconds. If the problem is the motion or I/O card, either of these can be replaced by anyone without disturbing the wires, control screens or logic. This is much easier than a pre-fab control since they have hard wiring and external PLC devices with ladder logic burned into them. With CamSoft the logic is running in the computer. The handheld controller is also another good idea because it uses a standard long printer cable that can be unplugged by the user and replaced in 5 seconds. The handheld controller replaces all the operator interface buttons, lights, knobs and handwheel. The computer's keyboard or touch screen contains the rest. Keep in mind that we also provide remote and self-diagnostic software to each customer. Think of it this way, keep on hand an off-the-shelf computer from the store and any other spare parts you need. If a control breaks, you can swap out the broken computer with a new computer to replace any control for any machine type at anytime. You just have to save the CBK file onto a floppy disk to restore that particular operator screen, G codes, M codes and logic.
What about maintenance and repair?
Maintenance and repair are no longer an issue. Be the master of your own machine. Self diagnostics are part of each system. When it comes to parts, you can use off-the-shelf Windows based personal computers and brand name hardware purchased from local sources. Are your parts now either so proprietary or hard to find that they don't exist anymore? How long can you be down? You shouldn't need to rely on others, we can teach you how to service, support, maintain, and upgrade the complete control and replace any part yourself.
How is logic programmed?
Unlike most other CNC controllers you do not need to purchase and program logic with third party software. We provide you with complete seamless digital I/O logic commands running in concert with the motion and other system logic on the PC itself totally within software. NO external PLC devices or ladder logic is needed. CamSoft offers a much easier logic programming method using simple commands that are referenced by terminal strip number or descriptive names. This method is preferred by installers that need to diagnose, modify and test the logic before they begin physical wiring. This is the only method that allows remote I/O logic diagnostics via a modem. We have our own I/O logic, which is much easier than learning PLC ladder logic. It even provides for very complex multiple I/O threads where as ladder is sequential and only branches off. Hundreds of every type of commands including IF THEN, LOOPS, TIMERS and WAITUNTIL are provided in simple to read text files that compile when the system starts. We utilize several manufacturers' I/O boards to give a wide choice of inputs/outputs. CamSoft wrote its own assembler drivers to access these cards in the unprecedented 10khz range.
Is there graphic CNC simulation?
We offer real time solid modeled or wireframe tool path simulation while the machine is cutting. Starting with Level-5 we offer tool path animation and CNC verification prior to pressing cycle start to verify what will happen prior to cutting the part. You have step by step control over each move graphically, moving the light source, solid model rotation and viewing angles.
What about service?
CamSoft has one of the best service departments in the business. You can always count on getting an answer via e-mail, fax or phone from a qualified technician immediately. If you need application assistance or custom logic, we have qualified in-house staff and local reps that can fulfill your needs either on-site or via the internet. Unlike other companies we do not detach ourselves from the hardware boards. CamSoft supports and takes responsibility for all of the hardware boards we sell you directly.